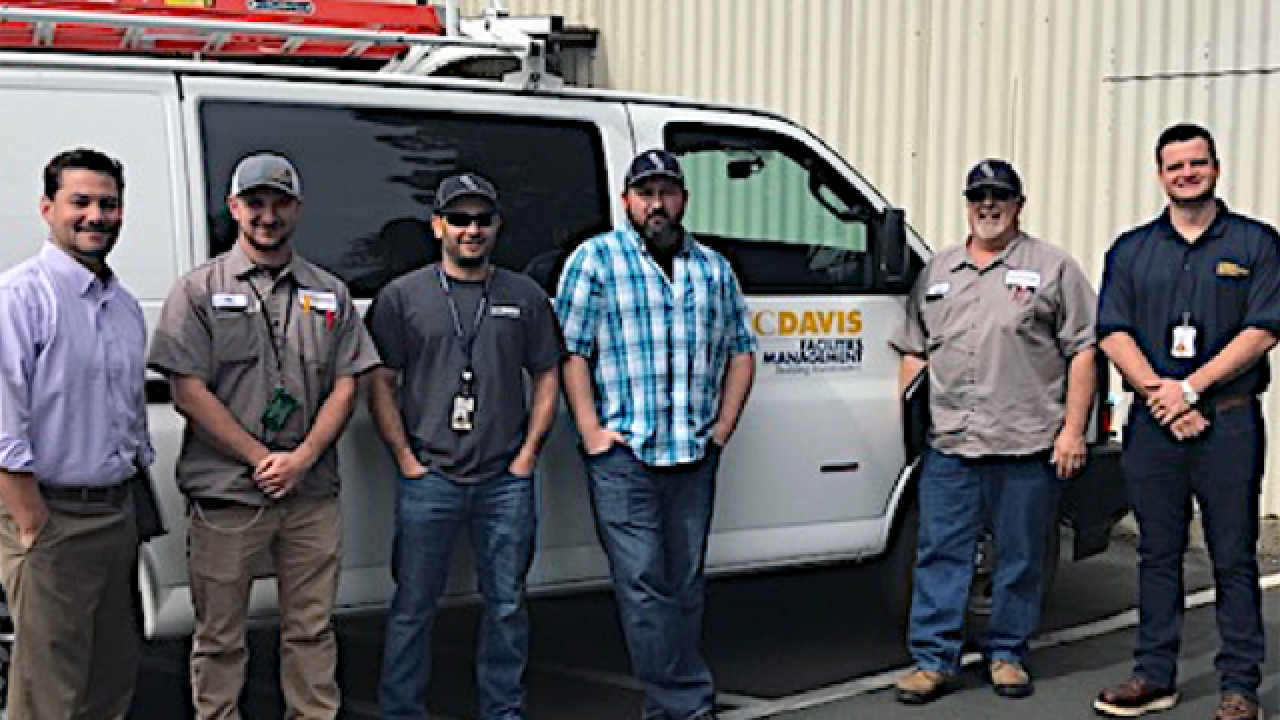
Increasing Wrench Time
Increasing Wrench Time
By redesigning the workflow for electrical repairs and upgrades, the project was able to potentially save 14,000 labor hours per year that could be redirected towards deferred maintenance.
UC Davis’s campus is comprised of more than 1,000 buildings of varying ages across 11.42 square miles. These buildings require a significant amount of work to maintain and renovate. But with resource and budget constraints, a question was proposed, “Could we increase available wrench time by decreasing the time trade professional spent on tasks that were not directly related to their trade?” (Wrench time is the time a tradesperson spends performing value-added work.)
To respond to this issue, Facilities, Supply Chain Management and the Office of Strategic Solutions formed a collaborative team to find solutions using Lean Six Sigma methodologies. The goal was to find efficiencies that would not only increase wrench time, but improve customer satisfaction and benefit everyone in the organization – not just an individual or one department. Communication had to be open and honest and employees were engaged to help identify issues and provide recommendations.
The dedicated project team consisted of:
- Eric Loveless, Supply Chain Management Supervisor
- Tony Vitone, Supply Chain Management Warehouse Personnel
- Joe Burns, Facilities Electrician
- Doug Mains, Facilities Foreman
- Aaron Knapek, Facilities Inspector, Planner, Estimator
- Hampton Sublett, Director of Strategic Solutions and Project Facilitator
The team first examined the current system for ordering, stocking, staging, and delivery electrical parts across campus. Locations were mapped where employees had to pull inventory, dispose of waste, and jobs sites. Time was measured for various tasks including ordering and delivering parts and materials, transportation of materials between sites, coordinating personnel, and implementation of job request.
After collecting and analyzing data, the team was able to work together to find multiple solutions to streamline the current process. By identifying the amount of time electricians spent acquiring the necessary parts and materials for each job, the team reduced the time on non-value added work for electricians by redesigning process flow. The new system required fewer trips for waste removal, lowered the number of return trips to pull inventory, realigned work among personnel to better utilize skills, and eliminated unnecessary tasks, allowing electricians to spend more time on the field and completing projects.
Increasing Wrench Time was a pilot program that took four months to conclude. This process of improvement will be taken into consideration as the team seeks to discover more solutions to improve service to the campus and increase employee satisfaction.
Eric Loveless stated it clearly, “Having an outlet to suggest new ideas and having the tools to explore those ideas within a dedicated team setting, has encouraged me to open my own way of thinking.” Loveless adds, “Its’ refreshing to be part of an organization that not only promotes change, but gives you the needed resources to accomplish that change.